How Solar Panels Can Impact Structural Integrity
Improperly installed solar panels are becoming a growing concern in pre-purchase inspections, often leading to structural performance issues. With the sharp rise in residential solar installations across Australia over the past decade, our inspectors have increasingly uncovered cases where poorly installed solar panels and other roof-mounted fixtures are compromising the structural performance of buildings.
Common Issues:
- Lack of proper bolting or strapping
- Incorrect installation which contravenes manufacturer specifications
- Installation companies failing to assess the roof structure before installation
In some instances, roof rectifications are required before a property sale can proceed.
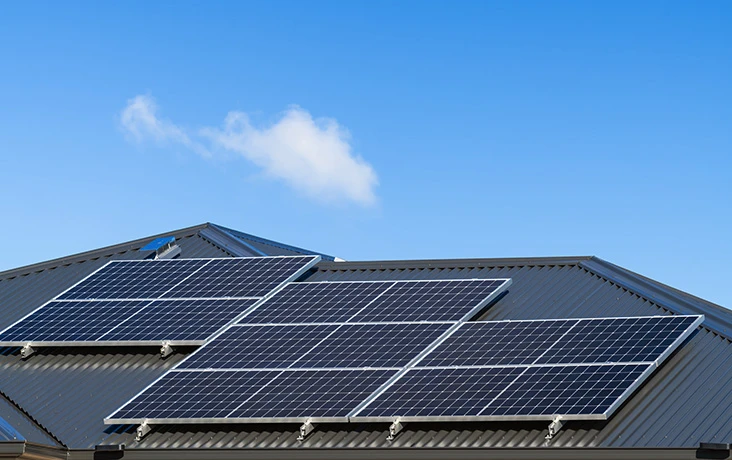
Case Study: Roof Structures
During a recent pre-purchase inspection, our inspector identified a critical defect in a second-story extension. One that could have had serious implications for both safety and structural performance.
This issue is linked to the increased use of rooftop installations (e.g. solar panels) over the last 10-15 years. A shift that was not common practice before approximately 2010.
The Issue
The timber top (or sole) plate was not properly fixed to the steel beams. Though the roof had stood for years without incident, this oversight posed a significant structural risk and failed to meet compliance standards as the extension was completed post 2012.
Why is this a problem?
As shown in the image below, the top plate should be secured to the I-Beam using M10 bolts to prevent slippage of the wood sole plate. If this anchoring is not completed during construction, the roof frame becomes vulnerable to structural movement, especially when additional weight is placed on the roof, such as a 6kW solar panel system weighing approximately 500 kg.
This extra weight increases lateral load distribution, and without proper anchoring, the unsecured top/sole plates can shift within the roof space. Over time, this leads to dangerous structural changes, potentially compromising the integrity of the entire roof.
The Lesson
Before installing any heavy items on a roof, it is crucial to verify the roof frames. Any trade performing rooftop installations must ensure the frame is properly secured to prevent undetected movement that could lead to structural failure.
The same principle applies to air conditioning installers who cut rafters or supports without consulting an engineer first—an oversight that can lead to serious structural consequences.
The Solution
The top/sole plate needed to be properly anchored to the I-beam. Most I-beams come pre-drilled with holes specifically for this purpose, making it a straightforward fix if identified before any slippage occurs. A competent trade can complete this correction quickly and effectively.
In the recent inspection of the second-story extension, thanks to our trusted network of tradespeople, the seller was able to arrange remedial work within 24 hours. The timber plates were securely bolted to the beams, ensuring the structural integrity of the roof was restored. This quick fix provided peace of mind before settlement at a minimal cost.
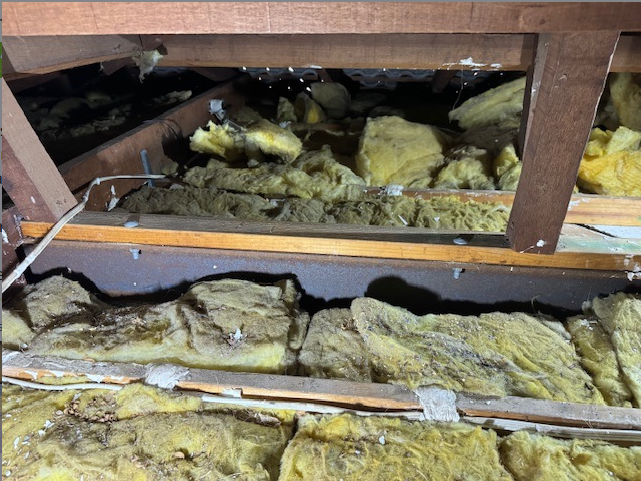
IMAGE: Timber Plate Secured to I-Beam After Remedial Works
Another Example
A recent case highlighted the importance of identifying these issues early. A property owner was quoted $3,900 to rectify a minor top/sole plate slippage that occurred after the installation of solar panels.
As a test case, one of BCI WA’s registered builders and the director attended the site and rectified the issue in just 1.5 hours. The total materials cost was only $38, and while we carried out this work free of charge, a fair price for this job, including materials and labour for two people, would be approximately $600 – $700, a fraction of the original quote.
This case highlights the importance of seeking expert advice before committing to costly repairs and ensuring issues are addressed promptly to prevent unnecessary expenses