‘Buyer Beware’. A term often used in the construction industry that means you as a homeowner need at minimum, a basic understanding of construction and what is ‘acceptable’ with regards to the Australian Standards, NCC, and The Australian Standards and Tolerances.
BCI WA recently conducted both a Slab Down Inspection and a Practical Completion Inspection (PCI) in Perth and our inspector described them as some of the worst he has ever seen. He is a registered builder with over 30 years of construction experience and approx. 9,500 building inspections under his belt.
These inspections uncovered serious construction defects, leaving the future homeowner facing delays of several months to a year.
Below, we break down:
- The key findings from a slab down and a practical completion inspection (PCI).
- Discuss why inspections should be completed before every progress payment.
- Show you what a PCI ‘should’ look like.
Slab Down Inspections - Uncovering Critical Early-Stage Issues
A slab-down inspection is a critical check after the concrete slab is poured to ensure it meets architectural plans and industry standards. In this case, the inspection revealed multiple major issues, raising concerns about the structural integrity of the build.
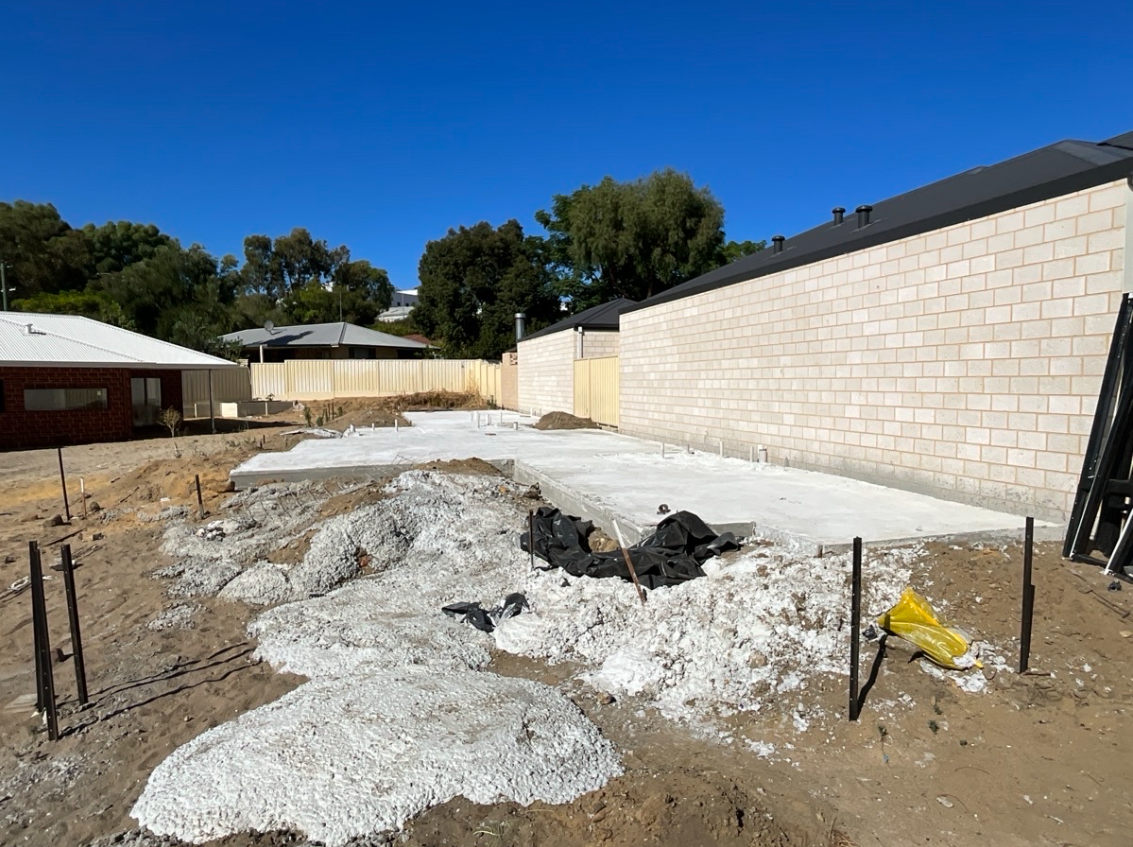
Slab Edge Heights & Wet Areas
The slab edge heights were inconsistent, measuring between 153mm and 160mm instead of the required 172mm. Additionally, wet area set-outs (WC, Bathroom, and Ensuite) did not align with the plans, indicating serious errors in execution.
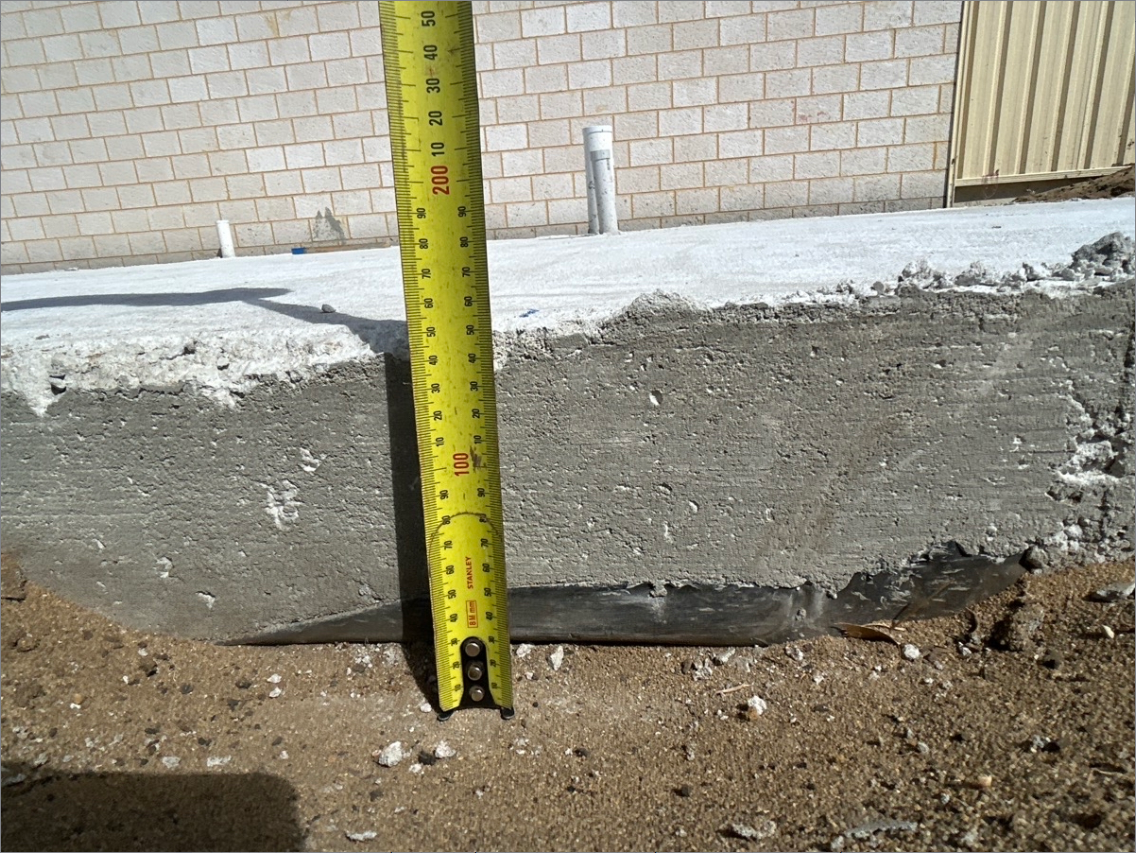
Plumbing & Electrical Services
Plumbing pre-lays were misaligned, including waste pipes in the Ensuite, WC, and vanity. These must be repositioned to match the design specifications, ensuring functionality and compliance.
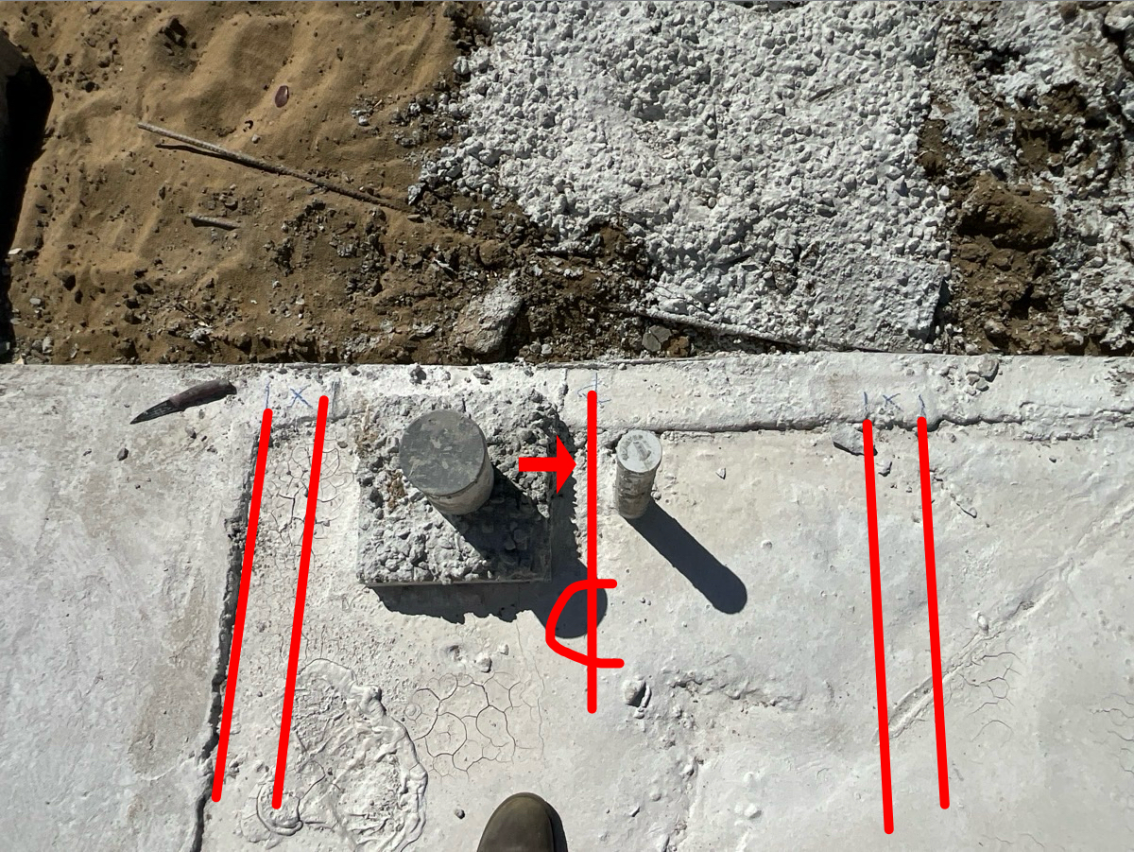
Concrete Quality & Surface Finish
The slab surface was not finished to industry standards, showing poor trowel work and uneven surfaces. This fails to meet WA Guide to Standards and Tolerances 2019, Section 2.10, requiring remedial works to bring it to an acceptable level.
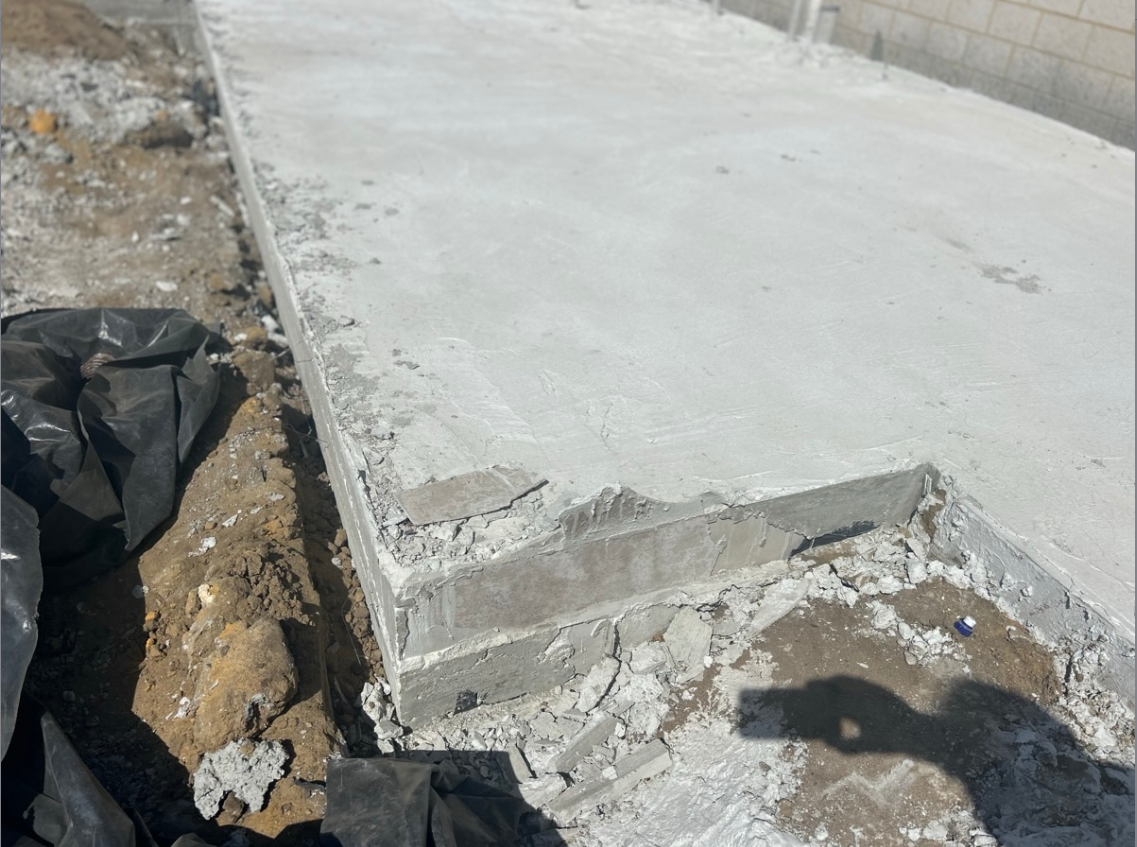
The Outcome
Given the severity of the defects, we advised the homeowner that a full slab removal and replacement was the best course of action. While the builder insisted they could rectify the issues, a structural engineer had to be engaged to assess the next steps. It remains unclear whether the builder took full responsibility for the costs, but this setback has delayed the home’s completion by months—possibly up to a year.
Practical Completion Inspections - When the Build Falls Short
A Practical Completion Inspection (PCI) is conducted before final payment to ensure the home is ready for handover. Many builders push for final payment before the home is actually complete, and in this case, the builder assured us everything was ready.
Our inspection told a very different story. The home was still at least two months away from completion, and instead of the usual four or five minor issues, we uncovered over 100 defects—clear proof that it was nowhere near finished.
Staircase Concerns
The staircase was incomplete and unsafe, with missing handrails, increasing the risk of falls. Makeshift steps had been installed but were not part of the final build, raising concerns about stability and are non-compliant.
Additionally, there was a significant deviation from the approved plans—15 steps (including winders) were specified, yet only 12 steps were constructed, failing to meet the design requirements.
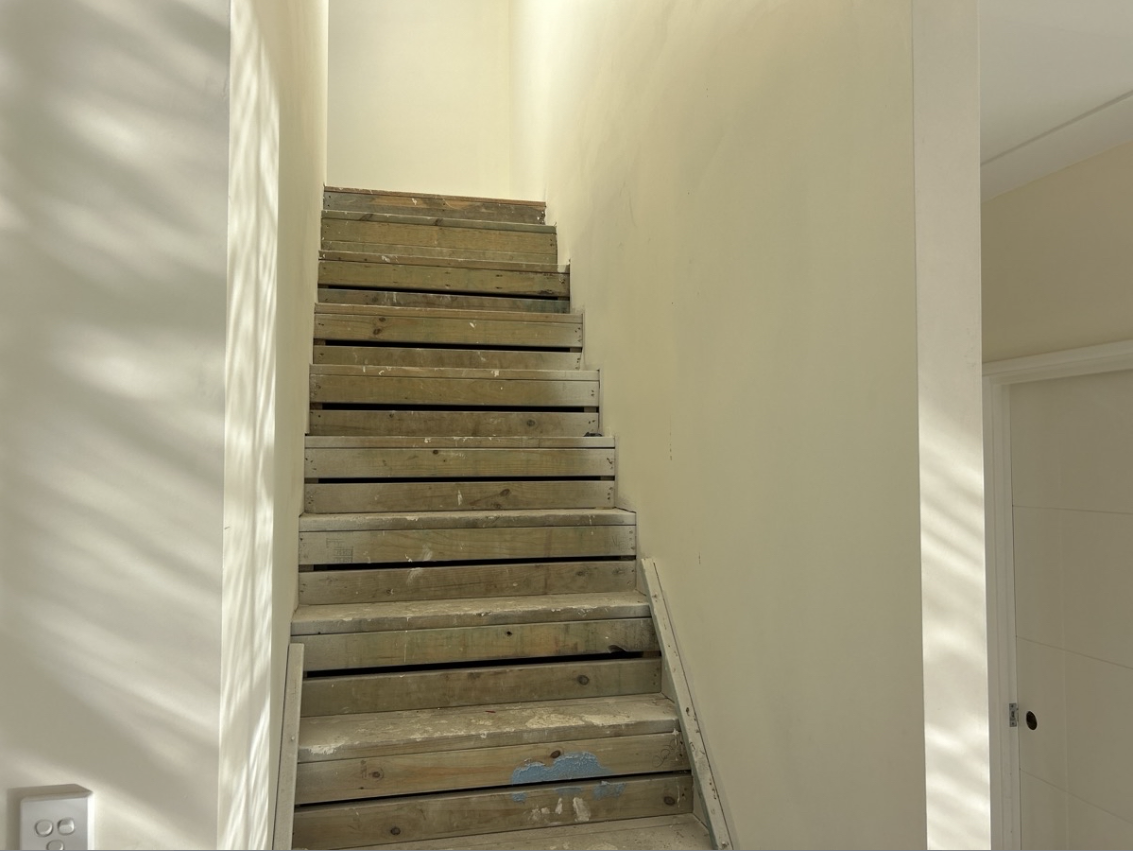
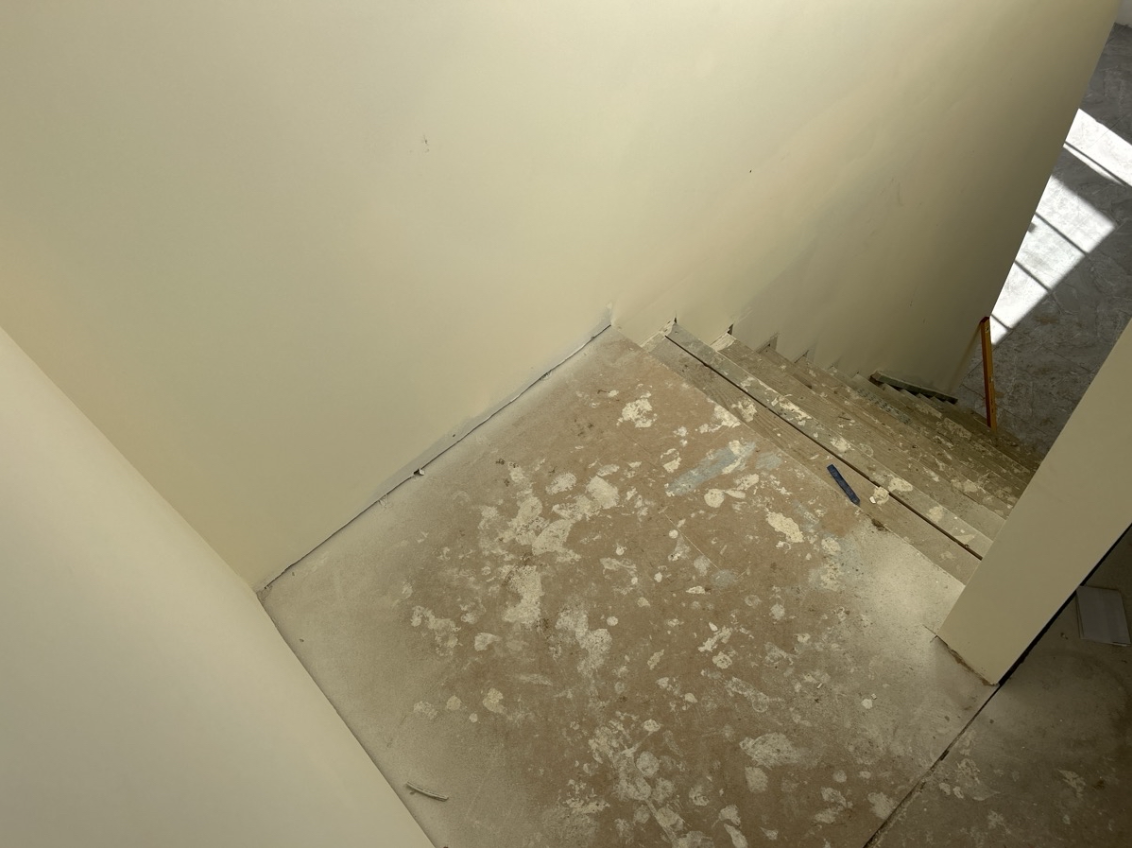
Major Issues Found in the Bathroom
The bathroom had multiple defects that required urgent attention. The floor levels were incorrect, creating a 25mm step down that needed correction. The waterproof membrane was breached at floor wastes, posing a significant risk of water damage. Additionally, lipping on floor and wall tiles was evident, impacting both aesthetics and safety, while uneven grout lines and poor tile workmanship further highlighted the substandard finish. The ceiling had only one coat of paint instead of the required two, and key fixtures such as cabinetry, the bath, shower screen, mirror, towel rails, and plumbing fittings were missing, leaving the space incomplete and far from practical completion.
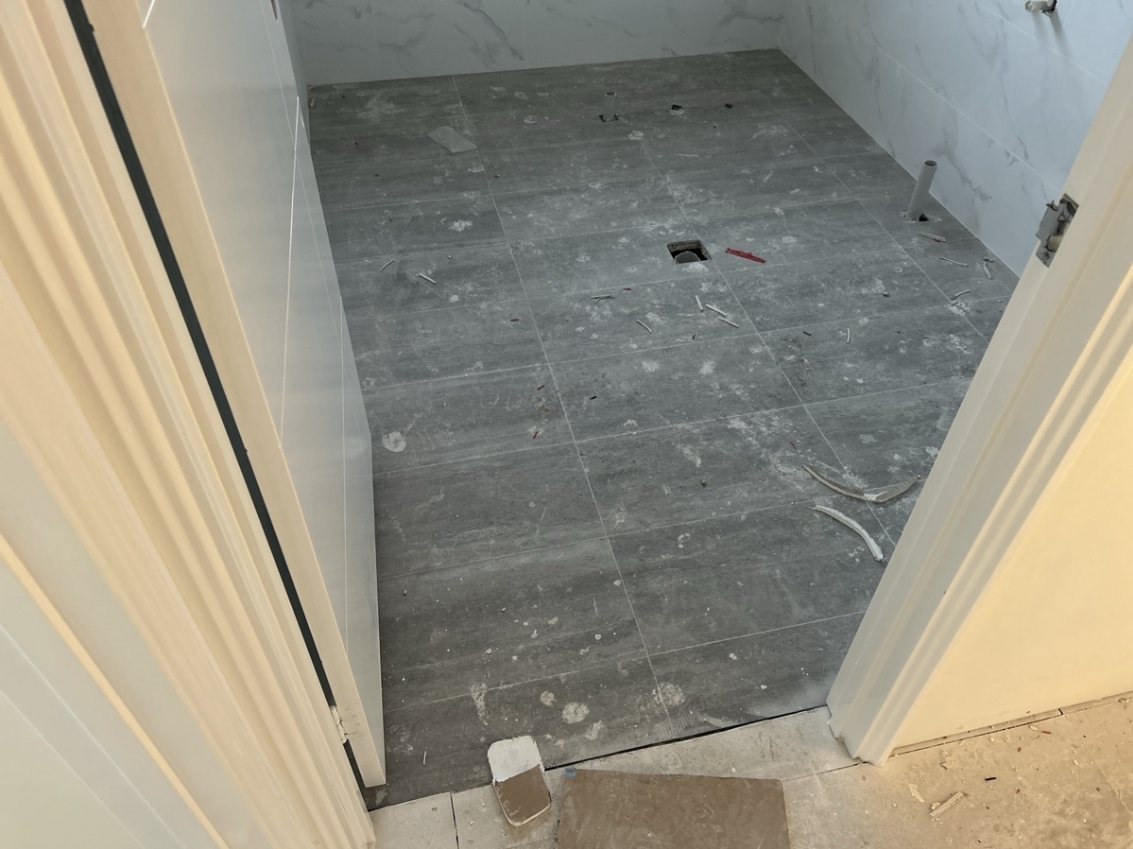
What a PCI Report Should Look Like
A PCI should focus on identifying minor workmanship issues, typically around 3 to 5 per room, which can be easily rectified within a few days (see example excerpt below). If the builder has done their job correctly, these issues should be minimal and not require extensive repairs.
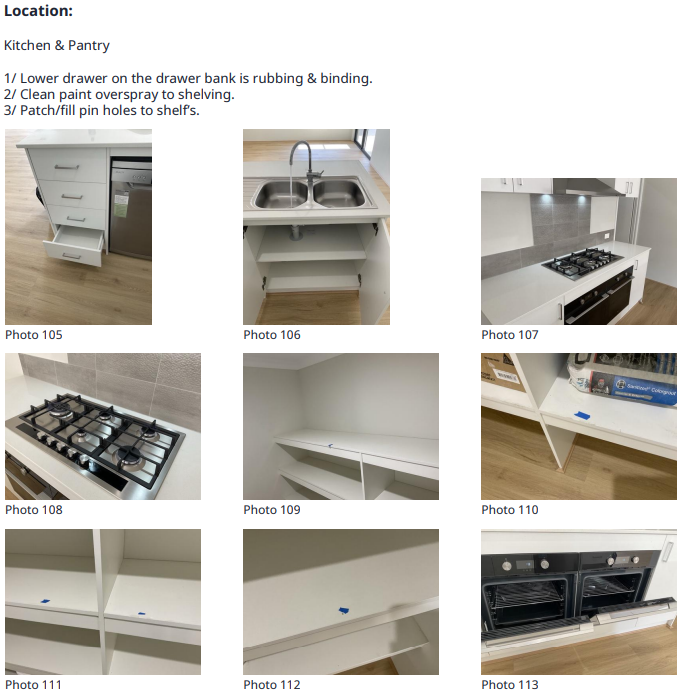
The build should be practically complete and ready for handover. There should be minor workmanship and painting or cabinetry issues to rectify and the builder should be aware of them or at least in agreeance that the minor defects should be rectified before handover. The process is 80% of the time amicable as professionals work together towards the same objective and end goal of handing over a building that has been built to the Australian standards, and building code, within standards and tolerance, and to the owner’s expectations.
Building a home should be an exciting and enjoyable process. Not faultless however professional and of a high standard. Our job as independent inspectors should be to be a fair and independent set of trained eyes that assists with minor defects that the supervisor may have overseen.
If you have questions regarding your build, please don’t hesitate to contact our office as verbal advice is free and we will help where we can without bias.